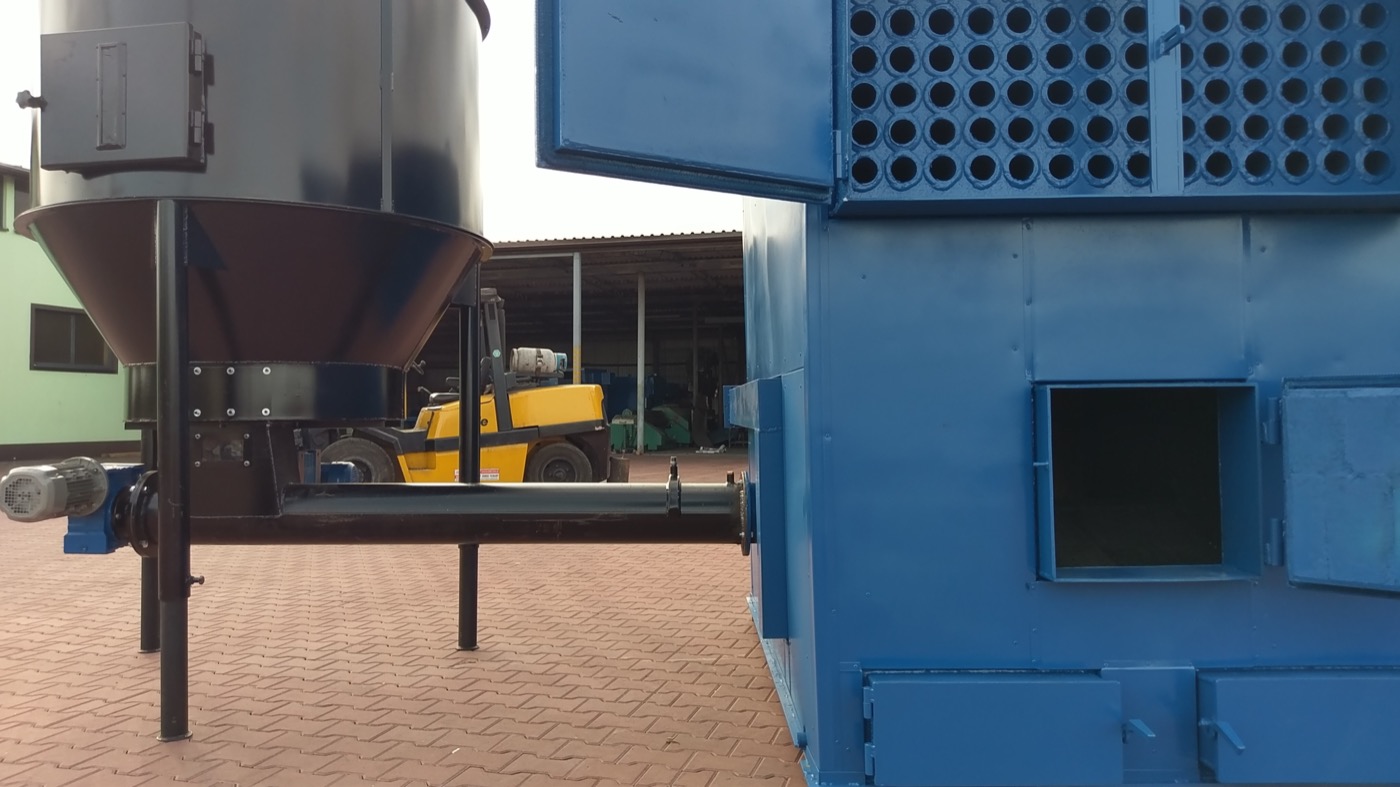
Samodzielne spalanie biomasy w kotłach przemysłowych dużej mocy, jest zagadnieniem trudnym, wymagającym wnikliwej analizy jej wpływu na konstrukcję i trwałość kotła. Paliwem spełniającym tutaj normy jakościowo jest zwykle pellet, lub toryfikat, jako paliwa o najwyższej jakości związanej z certyfikacją i przepisami branżowymi. Dość często wykorzystywane są też zrębki lub odpadki z przemysłu meblarskiego. W przypadku pozostałej biomasy najlepsze wyniki daje współspalanie w połączeniu z węglem kamiennym lub brunatnym. Związane jest to ze specyfiką biomasy, a w szczególności z jej stosunkowo niską wartością opałową, wysoką wilgotnością i zawartością substancji mineralnych (chlor, potas, sód) które ograniczają moc kotłów lub wręcz uniemożliwiają ich stabilną pracę. W poniższym artykule zostaną opisane kotły przemysłowe służące do współspalania biomasy oraz związane z tym problemy. Kotły dużych mocy do spalania samej biomasy będą tematem osobnego artykułu.
Wady i zalety biomasy jako paliwa
Biomasa w odróżnieniu do paliw kopalnych odznacza się dużą zmiennością składu chemicznego i wartości opałowej. Wiąże się to z szeregiem czynników fizycznych i biologicznych wpływających na wzrost biomasy, jak:
- wielkość opadów,
- nasłonecznienie,
- właściwości gleby,
- sposób nawożenia,
- częstotliwość nawożenia.
Nawet te same gatunki biologiczne wykazuje duże zróżnicowanie jakościowe na przestrzeni wielu lat, co utrudnia uzyskanie paliw o zunifikowanym składzie. Innym problemem biomasy jest jej bardzo wysoka wilgotność i stosunkowo mała gęstość przestrzenna zwiększająca wydatki związane z suszeniem i transportem. Przechowywanie biomasy w odróżnieniu do węgla musi się odbywać zawsze pod zadaszeniem, co zwiększa koszty, szczególnie w początkowym okresie inwestycyjnym, gdzie konieczne jest przygotowanie całej infrastruktury magazynowej.
Zaletą biomasy jest jej mniejsze zagrożenie dla środowiska przy spalaniu, z uwagi na niższą zawartość siarki niż w węglu. Popiół powstały po spalaniu biomasy ma wysokie właściwości nawozowe i może być wykorzystany rolniczo.
Wśród największych różnic pomiędzy biomasą a węglem należy wymienić:
- Jakościowo przybliżony skład chemiczny przy znacznych różnicach w składzie ilościowym
- Duże większa zawartość wilgoci w biomasie surowej co wpływa negatywnie na sprawność procesu spalania,
- Wysoka zawartość części lotnych w biomasie (2,5-krotnie wyższa niż w węglu kamiennym), co powoduje zmianę warunków zapłonu i spalania
- Zawartość azotu i siarki w biomasie jest niska, ale duża jest zawartość chloru, zwłaszcza w przypadku słomy, co bardzo zwiększa ryzyko korozji powierzchni ogrzewalnych,
- Większość rodzajów biopaliw stałych wykazuje stosunkowo niskie temperatury mięknięcia i topnienia popiołu w porównaniu z węglem, głównie z powodu dużej zawartości związków metali alkalicznych, wymaga to obniżania temperatury spalania w celu zapobieżenia szlakowania
- Niższa niż u węgla wartość opałowa zwłaszcza biomasy świeżej nie przesuszonej wstępnie,
- Niższa gęstość nasypowa biomasy w porównaniu do węgla wpływa na czas przebywania paliwa alternatywnego jakim jest biomasa w komorze paleniskowej
Tabela: Porównanie właściwości węgla i wybranych rodzajów biomasy.
Spalanie biomasy
Biomasę jako paliwo w energetyce można spalać w różnoraki sposób, najczęstszymi sposobami jest jej bezpośrednie spalanie w specjalnych kotłach ze złożem fluidalnym, które charakteryzują się bardzo dużą sprawnością podczas procesu spalania i stabilnymi warunkami pracy. Drugim najczęściej wykorzystywanym sposobem spalania biomasy jest jej współspalanie wraz z węglem w kotłach energetycznych pierwotnie zaprojektowanych do spalania węgla kamiennego bądź brunatnego. Dużo większym zainteresowaniem naszej krajowej energetyki i ciepłownictwa cieszy się drugi sposób spalania biomasy wraz z węglem w istniejących już blokach cieplnych. Rozwiązanie to wydaje się najkrótszą drogą, która zapewnia, że biomasa spalana w dużych kotłach energetycznych będzie wykorzystana jak najlepiej i stopień konwersji energii chemicznej w niej zawartej na energię elektryczną i cieplną będzie najwyższy.
W elektrowniach i elektrociepłowniach, w których realizuje się współspalanie biomasy z węglem, zauważamy kompensację okresowych zmian jakości i ilości biomasy a także stabilizację całego systemu paliwowego. Mimo to biomasa nadal budzi zastrzeżenia operatorów kotłów energetycznych. Spowodowane jest to wieloma problemami natury logistycznej z biomasą (relatywnie drogi transport i magazynowanie) a także występowanie problemów technicznych, wśród których należy wymienić: współmielenie oraz podawanie paliwa do kotła, powstawanie osadów na ścianach ekranów kotła oraz powierzchniach wymienników ciepła i innych elementach kotła (szlakowanie, osady sypkie, żużlowanie), spiekanie a także korozja chlorkowa i wysokotemperaturowa. Duża zawartość wilgoci w biomasie, jej niejednorodność i bardzo niska gęstość energetyczna (wartość opałowa biomasy wynosi 50% tej samej masy węgla, kiedy jej gęstość energetyczna stanowi 2 do 7% gęstości energetycznej węgla), a także utrudniony przemiał powodują, że udział współspalanej biomasy z reguły nie przekracza 10% udziału w strumieniu paliwa do paleniska. Trudności współspalania biomasy narastają wraz ze wzrostem udziału biomasy (przede wszystkim gdy stosuje się niskiej jakości biomasę w bezpośrednim współspalaniu z węglem) . Biomasa jest paliwem o słabych właściwościach przemiałowych, może posiadać wysoką zawartość chloru, posiada własności hydrofilowe, jej popioły mają niską temperaturę topnienia, co prowadzi do szlakowania kotła. Istnieje wiele sposób zapobiegania wyżej wymienionym problemom wśród których można wymienić:
- wymiana zniszczonego urządzenia, mechaniczne usuwanie osadów,
- czyszczenie złoża fluidalnego,
- intensyfikacja procesu poprzez dodawanie związków chemicznych,
- zmiana bądź dodanie nowego elementu do systemu instalacji cieplnej.
Niestety wszystkie te metody likwidują tylko zaistniałe skutki współspalania biomasy nie eliminując ich powstawania.
Proces współspalania biomasy w blokach cieplnych, w których znajdują się kotły pyłowe opalane i pierwotnie zaprojektowane na konwencjonalne paliwa węglowe i wytwarzające w wyniku tego spalania popiół, który ma często przeznaczenie do produkowania materiałów budowlanych, powoduje iż operatorzy tych kotłów muszą posiadać wiedzę na temat związku jaki ma udział biomasy na jakość powstających popiołów. Główne substancje mineralne w biomasie mają największy wpływ w procesach spalania, pirolizy i zgazowania. Najważniejszymi składnikami popiołów powstających ze spalania biomasy są: SiO2, CaO i K2O, natomiast węgla kamiennego są: Al2O3, SiO2, Fe2O3. Produkty uwalniane w trakcie termicznej przemiany biomasy (zwłaszcza słomy) wśród których są metale alkaiczne, siarka i chlor są głównym sprawcą tzw. korozji wysokotemperaturowej (o tym za chwilę). Niektóre składniki mineralne biomasy natomiast mogą być prekursorami katalizy bądź samymi katalizatorami procesów zgazowania i pirolizy (przykładem takim jest KCl w trakcie pirolizy słomy). Dzięki poprawnie dla danego rodzaju kotła dobranej biomasie i surowcu węglowym i zwróceniu uwagi na ich skład chemiczny, można kształtować właściwości powstającego w wyniku współspalania popiołu.
Zalety i wady współspalania biomasy
Zalety stosowania procesu współspalania biomasy:
- Proces współspalania podlega stabilizacji przez spalanie węgla
- Możliwość niemalże natychmiastowego wykorzystania biomasy w dużej skali
- Dużo niższe emisje tlenków azotu, dwutlenku siarki oraz dwutlenków azotu (dla paliw kopalnych), większa elastyczność kotła, brak uzależnienia produkcji energii elektrycznej od zapasów i dostępności biomasy (możliwość natychmiastowego przejścia na węgiel) co jest bardzo korzystnym zjawiskiem dla operatora systemu energetycznego
Wady stosowania współspalania biomasy:
- Kompleksowy proces wstępnego przygotowania biomasy (suszenie, rozdrabnianie) do jej współspalania, związane również z przygotowaniem odpowiedniej infrastruktury magazynowej
- Obniżenie sprawności i wydajności kotła
- Szereg efektów ubocznych takich jak szlakowanie powierzchni ogrzewalnych związanych ze składem substancji mineralnej biomasy.
Fot. Proces szlakowania kotła zasilanego biomasą
Szlakowanie - to powstawanie osadów na ściankach kotła, związane z charakterem popiołu. W przypadku biomasy, duża zawartość sodu i potasu w paliwie powoduje obniżenie temperatury topnienia popiołu, który tworzy twarde osady na powierzchniach wymiany ciepła. Ciekawostką jest, że spalanie samej biomasy nie wpływa znacząco na proces zarastania kotła, natomiast przy współspalaniu biomasy z węglem, proces szlakowania znacznie przyspiesza stając się zagrożeniem dla kotła. Warstwy osadów ograniczają wymianę ciepła, szczególnie w ciągu konwekcyjnym kotłów i przyczyniają się do wzrostu straty wylotowej kotłów. Ponadto mogą spowodować miejscowe przegrzewanie elementów ciśnieniowych. Proces odkładania się osadów pokazuje rys. obok a wygląd samej szlaki zdjęcie powyżej.
Główne problemy związane z negatywnym wpływem biomasy na zanieczyszczenie powierzchni ogrzewalnych kotła został scharakteryzowany i opisany poniżej:
- Dodawanie paliwa o niższej wartości opałowej i wyższej zawartości wilgoci, jakim jest biomasa drzewna, powoduje wzrost strumienia wody wtryskowej, który przy dostarczaniu 20% paliwa biomasy do głównego strumienia paliwa jaki kierowany jest do palników wzrasta o 50% w stosunku do stanu podczas spalania samego węgla. W celu rozwiązania tego problemu stosuje się zasilanie drewnem dolnych palników kotła aby obniżyć jadro płomienia, czasem niestety konieczna jest rozbudowa instalacji wtryskowej.
- Współspalając z węglem biomasę typu słoma należy brać pod uwagę fakt, że charakteryzują się one niską zawartością substancji mineralnych co powoduje, że w trakcie współspalania uzyskuje się zmniejszony strumień popiołu pomimo powiększenia łącznego strumienia paliwa.
- Współspalanie słomy wywiera najmniejszy wpływ na wymianę ciepła w kotle. Słoma natomiast spalana razem z węglem powoduje poważne zagrożenie korozją wysokotemperaturową chlorkową.
Na zdjęciu po korozja wysokotemperaturowa.
Korozja chlorkowa - Zawartość chloru w słomie, w zależności od jej rodzaju, może być nawet pięciokrotnie wyższa niż dla węgla kamiennego. Powstałe chlorki żelaza dyfundują do powstałej na powierzchni przewodów warstwy tlenków żelaza (Fe3O4) osłabiając miejscowo strukturę. W wyniku tego procesu od rur potrafią odłączać się sporych rozmiarów płaty tlenku żelaza powodując pocienienie materiału. Przyczynia się to do zwiększenia częstotliwości rozszczelnienia instalacji w ciągu konwekcyjnym. Cały proces ulega nasileniu w połączeniu z pojawieniem się grubej warstwy osadów, powstałych w procesie współspalania, (szlaki). Próba jej oddzielenia może powodować dodatkowe ścienienie ścianek przewodów i stać się przyczyną nieszczelności kotła.
Problem ten można rozwiązać poprzez właściwe dobranie charakterystyki węgla.
- Niemalże wszystkie typy biomasy drzewnej charakteryzują się dużo większą aniżeli węgiel skłonnością do tworzenia osadów popiołowych. Wynikiem tego jest podwyższenie straty wylotowej i spadek sprawności kotła.
- Zanieczyszczenia kotłów podczas współspalania biomasy z węglem można ograniczyć stosując specjalnie przygotowane zdmuchiwanie popiołu.
Badania i obserwacje na kotłach przemysłowych (np. OP-210, OP-380) pokazują, że:
Przy niewielkich udziałach biomasy (do 12%) wyraźnie można zauważyć obniżenie emisji pyłów oraz związków siarki. Jednocześnie, na analizowanych jednostkach nie zauważa się znaczącego przyspieszenia procesu szlakowania i osadzania się zanieczyszczeń na powierzchniach ogrzewalnych. Powyżej 12% masowego udziału biomasy w składzie mieszanki, zauważalne jest przyspieszenie powstawania niekorzystnych zjawisk jak szlakowanie, przyspieszenie erozji, pojawienie się ognisk korozji. Wzrost udziału biomasy w strumieniu paliwa powyżej 30%, zwiększa ryzyko pojawienia się szkodliwych zjawisk, a w rezultacie częstszych nieplanowanych odstawień kotła z ruchu w celu usunięcia awarii i czyszczenia powierzchni ogrzewalnych. Portal energetykacieplna.pl w artykule "Wady i zalety spalania biomasy w kotłach energetycznych" i przeprowadzonej analizy kotłów przemysłowych udowadnia, że ilość spalanej biomasy w kotłach nie powodująca istotnej zmiany procesu spalania zależy od ich mocy. W kotłach OP-210÷OP-230 nie należy np. więcej spalać biomasy jak 6%, w kotłach OP-380÷OP-430 nie więcej jak 9%, w kotłach OP-650 o normalnej komorze nie więcej jak 10%, w kotłach OP-650 z powiększoną komorą nie więcej jak 12%, a w kotłach szybowych OB-1150 nie więcej jak 13% udziału masowego.
Jeśli popiół z kotła ma wykorzystanie do produkcji materiałów budowlanych (cement popiołowy, beton komórkowy) ilość współspalanej biomasy nie powinna przekraczać 6% (wyniki konferencji naukowo-technicznej „Współspalanie biomasy i paliw wtórnych w kotłach energetycznych" zorganizowanej prze Izbę Gospodarczą Energetyki i Ochrony Środowiska oraz Instytut Energetyki w dniach 12 — 14 maja 2004 w Zakopanem).
Metody współspalania biomasy z węglem
METODA 1 - Bezpośrednie współspalanie biomasy jest stosowane w momencie, gdy w trakcie procesu spalania, który jest realizowany w jednej komorze paleniskowej strumienie biomasy i węgla są dostarczane oddzielnie lub też, co jest bardzo szeroko stosowane w naszej krajowej energetyce wcześniej przygotowana jest mieszanka biomasy i węgla. Jest to najczęściej stosowany sposób współspalania paliw alternatywnych z paliwami konwencjonalnymi w Polsce i związane jest to z niskimi kosztami inwestycyjnymi, które należy ponieść w celu modernizacji istniejących bloków energetycznych.
METODA 2 - Pośrednie współspalanie, jest realizowane w momencie, gdy:
- przeprowadzone jest zgazowanie biomasy w specjalnym gazogeneratorze, a powstający gaz jest transportowany do komory paleniskowej, gdzie w specjalnych palnikach gazowych ulega spaleniu
- spalanie biomasy jest przeprowadzane w przedpalenisku, a entalpia zawarta w powstających spalinach jest wykorzystywana w bezpośrednio w wymiennikach ciepła lub w komorze spalania. Układy, które wykorzystują instalacje do procesu pirolizy, gazyfikacji bądź przedpaleniska są mało popularne. Mimo, tego iż posiadają one wiele zalet takich jak między innymi sposobności utrzymania wymaganej przez zewnętrznych odbiorców jakości popiołu z procesu współspalania biomasy dzięki rozdzieleniu strumienia popiołu z danych paliw oraz możliwości wykorzystania na procesy energetyczne niekonwencjonalnych paliw, które są wytwarzane z odpadów przemysłowych czy też komunalnych bez zagrożenia powierzchni ogrzewalnych kotła agresywnym środowiskiem osadów i spalin, układy tego typu są bardzo drogie w wprowadzeniu .
METODA 3 - Współspalanie w układzie równoległym to taki rodzaj współspalania, w którym każde paliwo zarówno węgiel jak i biomasa są spalane w oddzielnych komorach spalania, w których proces spalania przebiega w sposób indywidualnie przygotowany i kontrolowany. Jednym z przykładów współspalania równoległego jest układ hybrydowy, który opisuje się jako specjalny układ jednostek wykorzystujących do współspalania specjalnie przygotowaną biomasę i węgiel oraz produkujących parę na wspólnym kolektorze parowym. Zazwyczaj proces współspalania w systemie hybrydowym stosowany jest dla kotłów pracujących w zakładach papierniczo-celulozowych
Kotły do spalania biomasy
RODZAJE KOTŁÓW ENERGETYCZNYCH WYKORZYSTYWANYCH DO SPALANIA I WSPÓŁSPALANIA BIOMASY
W Polsce najczęściej spotykanymi typami kotłów energetycznych większej mocy, w których spalana jest biomasa są trzy rodzaje kotłów:
- kotły fluidalne
- kotły pyłowe
- kotły rusztowe
Kotły fluidalne FBC - są to najnowocześniejsze rodzaje kotłów charakteryzujące się najwyższymi parametrami pracy i najlepszą sprawnością w trakcie procesu spalania dochodzącą do ponad 80%. Paliwo w tych kotłach spala się w postaci zawieszonej, dlatego musi być dobrze rozdrobnione. Postać zawieszoną uzyskuję sie dobierając w odpowiedni sposób prędkość przepływu powietrza przez komorę spalania tak, aby była ona większa niż prędkość opadania cząsteczek paliwa i dodatkowego materiału inertnego. Materiał inertny tworzy piasek i dodatkowo popiół powstały po spaleniu i ma za zadanie równomiernie rozprowadzać temperaturę po całej komorze spalania, dzięki czemu nie ma stref temperaturowych typowych przy spalaniu płomieniowym. Temperatura spalania w kotle fluidalnym jest dzięki temu niższa i nie przekracza 900C, co znacznie ogranicza emisję tlenków azotu NOx oraz tlenków siarki. Te ostatnie można wychwytywać stosując dodatkowo w materiale inertnym sorbent z kamienia wapiennego który wiąże siarkę bezpośrednio w złożu. Odsiarczanie metodą wapienną sięga 50-98%, daje to możliwość spalania również paliw o znacznej zawartości siarki. Niestety, spalanie w niskich temperaturach ma też swoje wady, powoduje wzrost emisji wielopierścieniowych węglowodorów aromatycznych WWA. Innym problemem jest produkcja dużej ilości siarczanu wapnia. Większość polskich elektrowni radzi sobie z tym tworząc przyzakładową produkcję wyrobów gipsowych głównie płyt gipsowo-kartonowych.
Rys. Schematy kotłów fluidalnych. Po lewej ze złożem stacjonarnym pęcherzykowym,
po prawej ze złożem cyrkulującym.
Podział kotłów fluidalnych
Podstawowego podziału kotłów fluidyzacyjnych dokonano ze względu na prędkość przepływającego czynnika w komorze spalania, skład frakcyjny materiału stanowiącego warstwę fluidalną oraz ciśnienia panującego w komorze paleniskowej. Pod tymi względami kotły fluidyzacyjne dzielimy na:
- kotły fluidyzacyjne ze złożem stacjonarnym (pęcherzykowym) – w literaturze anglosaskiej oznaczane jako AFBC (Atmosferic Fluidized Bed Combustion),
- kotły fluidyzacyjne z ciśnieniowym złożem stacjonarnym (pęcherzykowym) – PFCB (Pressurized Fluidized Bed Combustion),
- kotły fluidyzacyjne ze złożem cyrkulacyjnym – CFBC (Circulating Fluidized Bed Combustion),
- kotły fluidyzacyjne z ciśnieniowym złożem cyrkulacyjnym – PCFB (Pressurized Circulating Fluidized Bed Combustion).
Charakterystyka kotłów fluidalnych
Kotły z paleniskiem stacjonarnym - w kotłach tego typu materiał inertny nie cyrkuluje pozostając cały czas w postaci zawieszonej w komorze spalania. Wymaga to stałej kontroli prędkości przepływu powietrza.
Rys. Kocioł z paleniskiem pęcherzykowym stacjonarnym.
Rys. Kocioł fluidalny ze złożem cyrkulującym cyklonowym.
Kotły fluidalne cyrkulacyjne - prędkość przepływu powietrza jest tutaj tak dobrana, aby część piasku stanowiącego złoże była unoszona i przemieszczana w przestrzeni kotła. Złoże kolejno trafia do cyklonów, a następnie z powrotem do kotła poprzez kanał recyrkulacyjny. Kotły z cyrkulującym złożem stosuje się w instalacjach o dużej przepustowości.
Podwyższona prędkość powietrza fluidyzującego powoduje wzrost turbulencji w kotle zwiększając przez to parametry wymiany ciepła pomiędzy spalanymi cząsteczkami biomasy a powierzchniami ogrzewalnymi kotła.
Schematy kotłów z cyrkulacyjną warstwą fluidalną (rys. poniżej):
a) kocioł typu Ahlstrom,
b) kocioł typu Lurgi,
c) kocioł z binarną warstwą fluidalną,
d) kocioł z paleniskiem Circofluid.
Charakterystyczne cechy konstrukcyjne kotłów z cyrkulacyjną warstwą fluidalną przedstawiono na powyższym rysunku. Głównymi elementami składowymi typowego kotła z cyrkulacyjna warstwą fluidalną są: komora paleniskowa, cyklon, układ nawrotu z zamknięciem syfonowym lub zaworem typu L. Niektóre rozwiązania kotłów (rys. b i rys. c) wyposażone są w tzw. zewnętrzny wymiennik ciepła. Komora paleniskowa wyposażona jest w szczelne, membranowe powierzchnie wymiany ciepła, natomiast dolna część komory paleniskowej wyłożona jest masą ogniotrwałą. W tej części komory znajdują się także otwory dla wprowadzania paliwa, sorbentu, wtórnego powietrza, popiołu zawracanego spod cyklonu, palników rozpałkowych oraz odprowadzania popiołu. Spalanie paliwa zachodzi na ogół w dolnej części komory paleniskowej, podczas gdy przekazywanie ciepła do ścian odbywa się w górnej części komory, głównie drogą promieniowania i konwekcji ziaren materiału sypkiego.
Cyklon, na ogół wyłożony masą ogniotrwałą przewidziany jest dla oddzielenia ziaren materiału sypkiego unoszonych z gorącymi spalinami i zawrócenia ich z powrotem na dno komory paleniskowej, poprzez rurę opadową i syfon. Syfon przeznaczony jest dla zabezpieczenia przed wstecznym przepływem spalin z komory paleniskowej do cyklonu.
Prędkość gazu, z jaką przepływa on przez komorę paleniskową zwykle mieści się w przedziale 4,5 do 6 m/s. Powietrze wprowadzane do kotła jest sumą powietrza pierwotnego, wtórnego, powietrza transportującego paliwo i sorbent, powietrza zamykającego w syfonie, powietrza fluidyzującego w zewnętrznym wymienniku oraz klasyfikatorze popiołu.
Klasyfikator popiołu odprowadzanego z dolnej części komory paleniskowej jest przewidziany dla wydzielenia z masy materiału sypkiego wypełniającego komorę paleniskową grubych ziaren popiołu w celu wyprowadzenia ich na zewnątrz kotła. Temperatura w komorze paleniskowej utrzymywana jest na poziomie 850÷900°C. Temperatura 850°C zapewnia optymalne warunki wiązania siarki.
Kotły pyłowe
Kotły pyłowe: najpopularniejsze typy kotłów wykorzystywane w polskiej energetyce zawodowej co potwierdza ich największy udział w zainstalowanej w naszym kraju mocy elektrycznej. Kotły pyłowe posiadają oddzielny układ podawania paliwa stosowany do doprowadzania biomasy i odpadów. Kotły pyłowe mają również bardzo nowoczesne instalacje do oczyszczania spalin, które pozwalają na spełnienie wymagań związanych z emisjami, gdyż współpracują bardzo często z instalacjami półsuchego i mokrego odsiarczania spalin.
Poniżej kocioł pyłowy z przedpaleniskiem do spalania biomasy opatentowany przez firmę Ecoenergia.
Rys. Kocioł pyłowy z przedpaleniskiem do spalania biomasy (Ecoenergia)
Zasada działania przedpaleniska do spalania biomasy
Zasada działania przedpaleniska polega na podawaniu do specjalnej komory spalania, izolowanej cieplnie za pomocą wymurówki szamotowej, paliwa w postaci rozdrobnionego drewna, np. drewna pochodzącego z tartaków lub z cięć sanitarnych w lasach. Zapłon paliwa odbywa się poprzez dostawiany do komory na czas rozruchu palnik rozpałkowy na dostępne w danym zakładzie paliwo rozpałkowe. Pozostałości po spaleniu biomasy kierowane są z rusztu do lejów pod rusztem i dalej do odżużlacza. Powietrze do spalania pobierane z instalacji współpracującego z przedpaleniskiem kotła tłoczone jest pod i nad ruszt schodkowy. Podciśnienie niezbędne do pracy przedpaleniska wytwarzane jest w komorze paleniskowej pracującego kotła pyłowego. Powstające w wyniku spalania biomasy gorące spaliny kierowane są do odpowiednio dobranych dysz spalin. Dzięki współdziałaniu przedpaleniska z kotłem pyłowym z palnikami o niskiej emisji tlenków azotu możliwe jest uzyskanie dalszej redukcji tych związków w spalinach wychodzących z kotła, a ciepło spalin z biomasy zostaje wykorzystane przez układ wodno-parowy kotła. Odpowiednia konstrukcja przedstawionego przedpaleniska zapobiega powstawaniu zakłóceń procesu spalania w komorze paleniskowej kotła podstawowego i nadaje się do zastosowania bez konieczności ingerencji w układ fundamentowania kotła.
W przedpalenisku spalana może być biomasa o szerokim zakresie wilgotności, kaloryczności, granulacji oraz pochodzenia. Nominalna moc cieplna wynosi od 5 do 15 MWt.
Stacjonarne przedpalenisko na biomasę jest rozwiązaniem autorskim firmy Ecoenergia Sp. z o.o. zarejestrowanym w Urzędzie Patentowym.